Diamond Engineering, a construction company, based in Grand Island, Nebraska operates a fleet of nearly four dozen vehicles.
Diamond Engineering has over 90 years of experience in a wide variety of construction. From Water, Sewer, and Storm Sewer mains to Plowing Cable, Trenching and Telecommunications to Sheet and Pile Driving, Box Culvert and Bridge building to Curb & Gutter, Parking Lot and Street Paving. As is typical for their line of work, its equipment and people are spread out over several job sites.
Azuga’s customers in the construction industry derive multiple advantages from Fleet Tracking: In this case, a big improvement to the bottom line was a 10% discount on the insurance premiums. But there are many others:
- Increase in productivity–monitoring to keep workers on task. Customers get alerted when a vehicle’s ignition is on or off. The extent of use of the assets on site helps them decide on moving around equipment and teams between work sites. It’s easy to view the information on a single or several work sites simultaneously. This too pushes up productivity.
- Fuel savings–cut needless idling before it burns a hole in profits. Review the mileage reports and check how fuel is being purchased. When idling is reduced, and unauthorized usage is stopped, fuel costs come down.
- Better scheduling of maintenance–alerts ensure that key maintenance activity stays on schedule. Reports help fleets track odometer reading and engine hours, as well as equipment usage–just what they need to plan their maintenance.
- Time and Money–track employee work hours, and also use of equipment at work site. The fleet’s billing accuracy goes up, there’s less room for uncertainty with the customer, and issuing invoices is easier and faster.
- Compliance with work site conditions–keep fleet vehicles out of restricted areas. Maintain compliance with Hours of Service.
- Protect business assets–ensure assets cannot be stolen; now fleets can have ignition alerts and geo-fences to protect them. There’s round-the-clock monitoring of any vehicle movement.
- Faster finding and deploying–company equipment is spread across job sites, and when there’s need to call for a particular machinery, it helps to be able to track it in minutes and to check if it can be assigned to the incoming task.
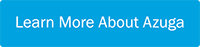
Diamond Engineering’s fleet has shown significant improvement in the area of speeding since implementing Azuga.
In Oct. 2016, Diamond’s speeding events per 100 miles, already low in comparison with other fleets, further decreased! Over the next few months, there was an 80% reduction in speeding events. Reduced speeding delivers better fuel use, and pushes up a fleet’s Safety Score.
"We brought data from the Azuga system to our insurance company. When they saw what we had in terms of the ability to locate our assets and monitor our driver behaviors, they were happy to work with us on our premium, and we got more than a 10% discount. We have the equipment and people all over the area. With Azuga, I know where everything is, and I know who’s using it on which job site and for how long."
Rod Gartner, President of Diamond Engineering,
Azuga is not just fleet tracking.
As a one-stop shop, we also provide Asset tracking to track construction equipment.
Azuga is a leading global connected vehicle platform, helping our customers turn data from vehicles and their use into intelligence that improves operations and safety while reducing cost and risk. Through its leading technology, the Azuga One platform, fleet applications, and data analytics, it provides customers–whether a small fleet of a few vehicles or up to several thousand–with robust features, ease-of-use, and affordable pricing.
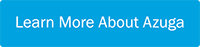